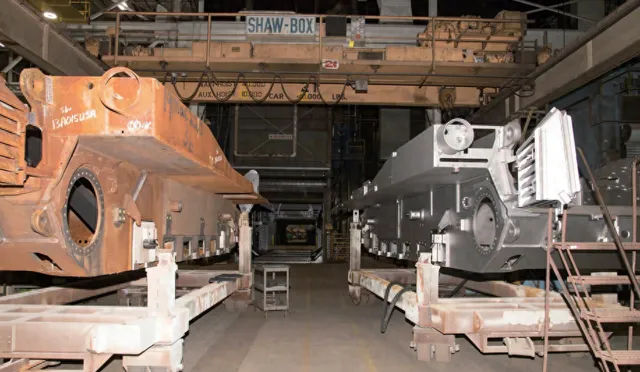
DOI:10.19486/j.cnki.11-1936/tj.2023.21.003
在近年來歐洲東部爆發的大規模沖突中,交戰雙方動用各種軍事手段展開激烈交鋒。地面作戰中,裝甲與反裝甲武器、裝甲與裝甲武器對抗尤為慘烈,雙方數千輛裝甲戰車被擊毀,裝甲兵傷亡慘重。這固然表明坦克裝甲車輛「陸戰之王」的地位依然穩固,但同時也意味著新一代地面作戰平台的研發需要加強裝甲防護技術的投入,裝甲鈦合金前沿技術探析也由此成為令人感興趣的話題。坦克裝甲車輛的基體裝甲材料應具有良好的抗彈效能、工藝效能和環境適應力能等。常見的金屬基體裝甲材料有裝甲鋼、裝甲鋁合金、裝甲鎂合金和裝甲鈦合金4種,其中裝甲鈦合金的綜合效能最優,能夠同時滿足抗彈效能、工藝效能和環境適應力能三方面的要求。事實上,高機動性、高防護能力與高可靠性必然是未來新一代裝甲車輛發展的重要方向,為了提高裝甲裝備作戰部隊的機動能力與生存能力,新型裝甲車輛需要滿足進一步輕量化與強防護的要求。與傳統裝甲鋼、裝甲鎂合金和裝甲鋁合金相比,裝甲鈦合金具有比強度高、抗彈效能好、焊接強度高、耐腐蝕等特點,被認為是新一代裝甲裝備實作顯著輕量化與強防護的優選材料。
背景
俄烏戰場的經驗表明,重型裝甲防護對於坦克裝甲車輛等地面作戰平台是至關重要的,但當前坦克裝甲車輛越來越重型化的趨勢卻令人十分不安。舉例來講,最新型的美軍M1A2C已經飆升到了73.6噸的水平,相當於兩輛59式坦克戰鬥全重的總和,如果以第二次世界大戰的標準,實際上已經邁入了超重戰車的門檻。誇張的噸位嚴重限制了坦克的戰術運輸能力,目前的救援車輛、戰術橋梁和重型裝置運輸車輛都無法承受M1A2C坦克的重量。美軍的絕大部份裝甲搶修車都拉不動「艾布拉姆斯」龐大的身軀。M88/M88A1所配備的絞盤只有45噸的拉力,在惡劣條件下(實戰中出事的時候往往就是惡劣條件)很難做到單車拉單車。而升級後的M88A2一方面數量還無法配齊,況且A2的絞盤也只有70噸的牽重力(不過可以靠滑輪組提升到140噸)。另外,超重的M1A2C還帶來了和平時期公路輸送違法的難題——軍事裝備在和平時期仍然要無條件地服從當地法律法規,但美軍現役的M1070重型拖車與M1000半掛車組合成的坦克運輸車有效載荷只有63.5噸,用於運輸M1A2C屬於嚴重超載。而且組合後整車重量已經超出了100噸,其軸重超出了歐洲國家的標準,也不能合法上路。嚴重超重另一個更為致命的尷尬是戰場機動問題,比如在其主要預設戰場的東歐地區,絕大部份民用橋梁在設計上都沒有考慮過30噸以上的車輛,甚至美軍的裝甲架橋車也難以支援M1A2C過河。基本型的M1A2就已經高達62噸,已經超出了美軍傳統突擊橋(M60AVLB使用的MLC-60橋)的60噸上限。當然,考慮到結構冗余,一般最大允許120%載荷,稍微超載一點也不會出什麽大問題,但重達73.6噸的M1A2C顯然已經將北約軍隊大部份現役架橋車的一切冗度全部用光。當然,不可否認,美軍M1074裝甲架橋車的MLC-95橋承載能力有95噸,似乎能夠應對73.6噸的M1A2C,但該突擊橋僅僅只有11公尺的跨度,戰場價值相當有限。究其原因,在於突擊橋本身也有著上限,這種上限主要體現在橋體品質上。一般來講,坦克架橋車的橋品質不得超過架橋車總重的26%。這種規定是有其現實原因的,金屬結構的橋梁無論是剪式還是平推式,都是呈兩截或者三截高高地堆在車體上,造成架橋車的車體重心非常高,影響其正常的野外行駛。為了避免裝甲架橋車頭重腳輕,就要限制橋體品質在全車品質中的比例。 另外,橋梁本身為金屬制成,而且大多是鋼鐵,為了確保其承重能力,不可避免地要使用更粗壯的結構來實作強度,這就導致橋梁等級越高,橋重越大。因此在同樣的材料情況下,要想實作荷載的突飛猛進,也就只能犧牲跨度了。可是沒有跨度的突擊橋,戰場價值有多高是不難想象的。除了裝甲架橋車外,舟橋部隊同樣會參與對前線的保障,而北約軍隊廣泛使用的M3舟橋車的設計標準也僅僅是允許60噸以內的履帶式車輛透過,在現有的技術水準下,73.6噸重的坦克對舟橋部隊實在是一個異常艱巨的挑戰。畢竟相比於突擊橋,舟橋受環境影響較大,本來就不應該去超標使用,M1A2C這樣超重噸位的坦克,很可能發展為一個反面教材的範例。一輛優秀的主力戰車首先得能在假想戰場上機動起來,作為沖擊的矛頭和反沖擊的鐵錘,而不是成為「能上前線就是好漢,可惜就是上不了前線」的遺憾。所以,各國在新一代地面作戰平台的指標規劃中,均將不降低防護力前提下的噸位控制放在了重要位置。而正是在這一背景下,要實作新一代坦克裝甲車輛高防護力、輕量化的設計目標,擴大裝甲鈦合金材料的套用被認為是重要的技術途徑之一。
抗彈效能、抗毀傷機理及當前套用情況
鈦合金(TC4)的比強度為199牛·米/千克,合金結構鋼(38CrSi)的比強度為124牛·米/千克,裝甲鋁合金的比強度為146牛·米/千克,鈦合金的比強度最高,在制造相同強度要求的結構與零件時,鈦合金比合金結構鋼及鋁合金均要輕。鈦合金因其較低的密度、較高的比強度和優異的抗疲勞效能等,成為裝甲車輛車體輕量化設計的理想材料。同時,鈦合金材料還具備良好的抗彈效能和防腐效能。事實上,鈦合金具有高的結構承載能力以及良好的抗彈效能,就使用效能而言是最佳的裝甲防護材料。與傳統的裝甲鋼、裝甲鋁合金等金屬裝甲材料相比,裝甲鈦合金不但具有較強的抗各種型別彈丸侵徹的能力,還具有抗彈丸多次打擊的能力。20世紀90年代,美國陸軍實驗室(ARL)先後開展了不同口徑破片模擬彈(FSP)、普通穿甲彈(AP)、穿甲燃燒彈(API)、次口徑穿甲彈(APDS)、脫殼穩翼穿甲彈(APDSFS)和聚能裝藥破甲彈(HEAT)等對不同厚度Ti6Al-4V合金板材的終點彈道侵徹實驗,得到了其極限擊穿速度。其中,長桿形穿甲彈侵徹鈦合金靶板的實驗表明,Ti-6Al-4V合金靶板的抗彈效能比均質裝甲鋼提高60%~80%。另外,復合裝甲結構單元的具體研究內容歷來是世界各軍事強國裝甲防護技術的核心,保密級別很高,但在鈦基復合裝甲結構單元的研究方面,從公開報道來看,以鈦合金材料為基體封裝而成的陶瓷/金屬復合裝甲結構單元,在長桿形脫殼穩翼穿甲彈丸侵徹靶板時具有較高的抗侵入作用。這些資料表明,鈦基復合裝甲結構單元在長桿形模擬穿甲彈丸的侵徹過程中發生嚴重的自侵蝕,並伴有彈丸侵徹路徑的偏轉。彈靶作用過程中長桿形彈丸這種響應特征使得鈦基復合裝甲結構單元表現出優異的抗彈效能。美國國防科技資訊中心(DTIC)在2003年釋出的報告中指出,鈦合金材料在裝甲防護領域的套用中常見的損傷破壞模式為絕熱剪下沖塞破壞和崩落破壞。即鈦及鈦合金材料在彈丸侵徹條件下,往往透過絕熱剪下局域化變形行為協調彈丸的擠鑿作用,並透過絕熱剪下帶及其帶內裂紋的擴充套件連線導致靶板被擊穿。在長桿形脫殼穩翼穿甲彈丸侵徹條件下,由於鈦合金靶板和彈丸之間較強的互侵蝕作用,靶板彈坑邊緣大量的絕熱剪下帶萌生擴充套件並進而在帶內微裂紋的擴充套件連線過程下發生破碎,因此使得彈丸侵入鈦合金靶板後能量被大量消耗。鈦合金車體在同等外形條件下,透過數值計算及靶試試驗,典型抗彈部位總品質比鋁合金車體輕13%。相同品質下防護效能比鋁合金裝甲提高15%。以12公釐的TC4裝甲鈦合金為例,在同等防護條件下,相當於30公釐厚的裝甲鋁合金,減重效率35%。事實上,鈦合金具有密度低、比強度高、低溫韌性好、耐腐蝕等優點,是一種效能優良的結構裝甲材料。早在20世紀50年代,美國對鈦合金在兵器工業中的套用就開始發力,成果豐碩,為了減輕裝甲車的品質,提高其機動靈活性和抗彈能力,沃特敦(Watertown)兵工廠針對鈦合金抗槍彈和穿甲彈能力以及焊接效能進行了大量試驗,認為鈦合金是一種堅強的裝甲材料。1953年,美國陸軍在底特律(Detroit)兵工廠對用厚15.88公釐RC-130AW鈦合金板制造的T55型裝甲車的頂裝甲,以37公釐穿甲彈進行試驗,各項指標均合格,達到或超過預定值。1956年,美國用Ti-6Al-6V-2Sn-0.5Fe0.5Cu合金鍛造坦克履帶和坦克負重輪,裝於50噸坦克上透過了3379千米的野外跑路試驗,狀態良好。美國沃特敦兵工廠用Ti-6Al-4V和Ti-4Al-4V合金為坦克汽車司令部的M-21(XM-13)型指揮車各焊制了一個指揮塔,並用20公釐炮彈進行了實彈射擊。試射用了兩種速度,一種為450公尺/秒,沒有射穿,但是板的背面出現了不少小裂紋; 第二種射擊速度為504公尺/秒,穿入鈦板,但未穿透,卡在板內,裂紋也沒有擴充套件。試射結果都令人滿意,鈦合金炮塔的品質177千克,而鋼炮塔的為281千克,前者比後者輕37%。此外,沃特敦兵工廠還用Ti-6Al-4V合金和Ti-6Al-4Mn合金代替鋼制造的零件有:主動軸、懸掛臂、拖桿、扭力軸、前輪軸等,主動軸為Ti-6Al-4V合金的坦克進行了9654千米的野外試跑,狀態良好。該廠用Ti-6Al-4V合金鍛造的T109型坦克的履帶系統有:履帶板、緊固螺釘、中心導塊、導塊的邊、鏈等。鈦合金履帶板與橡膠的粘接性比與鋼的好一些而且品質比鋼件的約輕40%。經表面處理後的鈦合金履帶板在中戰車上進行了1352千米的野外試跑,完全達到預期效果。
當前,隨著材料技術的進步,現役裝備的升級改進中裝甲鈦合金材料已經有了更大規模的套用。美國與俄羅斯等國家已將裝甲鈦合金成功套用於多種坦克裝甲裝備,並且取得了顯著的輕量化效果。美軍先後在改造的M1「艾布拉姆斯」主力戰車、M2「布雷德利」步兵戰車以及「斯特賴克」輪式裝甲車等裝甲車輛上實作了裝甲鈦合金材料部件的規模套用,取得了明顯的減重和防護效果。以M1A2主力戰車為例,美軍先後對M1A2主力戰車進行了2個階段的升級改造。第1個階段完成於20世紀90年代,透過使用鈦合金替代發動機頂蓋、回轉炮塔頂蓋、主瞄具罩、指揮艙蓋、熱像觀測儀蓋、防核生化護蓋以及炮塔樞軸架等鋼制構件,獲得29.9%的綜合減重效果(420千克)。第2階段完成於21世紀初期,透過使用Ti-6Al-4V合金焊接而成的炮塔替代鋼制炮塔,獲得了4噸的顯著減重效果。美國陸軍還采用101.6公釐厚Ti-6Al-4V裝甲鈦合金制造了M2A4「布雷德利」步兵戰車指揮艙蓋和頂部防攻擊裝甲部件,獲得35%的減重效果;采用Ti-6Al-4V裝甲鈦合金制造了「斯特賴克」輪式裝甲車的鍛環;采用裝甲鈦合金制造了新一代AMPV裝甲運輸車的附加裝甲,大幅增強了防大口徑彈藥的能力;采用15.9公釐厚裝甲鈦合金制造了M10「布克」輕戰車的頂部裝甲,滿足了輕量化與強防護的要求。除美國外,其他主要軍事工業國家也在將裝甲鈦合金材料套用於坦克裝甲車輛設計制造中取得了可觀進展。比如,俄羅斯采用BT6、BT1-0等裝甲鈦合金制造了T-80主力戰車發動機外殼門、炮塔回轉支架等構件,較鋼質結構取得了40%以上的減重效果;采用裝甲鈦合金制造了T-90A主力戰車炮塔「碎片」復合裝甲框架及「碗型」無底金屬結,使其炮塔正面抗擊能力達到了1300公釐厚均質裝甲鋼水平;采用裝甲鈦合金制造了T-95主力戰車樣車模組化裝甲,使其炮塔正面抗擊能力達到了1500公釐厚均質裝甲鋼水平;法國采用裝甲鈦合金制造了VBCI的無人炮塔附加裝甲,使其炮塔的防護效能大幅提高,能夠防禦155公釐炮彈碎片和中/小口徑炮彈;英國采用裝甲鈦合金制造了改進型「武士」步兵戰車炮塔附加間隔裝甲,使其炮塔的防護效能得到明顯改善,能防禦30公釐尾翼穩定脫殼穿甲彈;加拿大采用裝甲鈦合金制造了MTVL側面披掛裝甲,使其抗彈等級由防禦7.62公釐穿甲彈提高到防禦14.5公釐穿甲彈。
與當前裝甲鈦合金材料在主要軍事工業國家現役坦克裝甲車輛上的套用情況相對應,各國已經建立起了各自的裝甲鈦合金軍用標準,比如20世紀50年代末,美國形成了全球第一個可焊接裝甲鈦合金材料的軍用標準MIL-A-46077。海灣戰爭後,美國陸軍材料實驗室深入研究了Ti-6Al-4V合金中主元素、間隙元素以及板材的熱處理工藝等對其抗彈效能的影響。1998年,美國頒布了可焊接裝甲鈦合金板材軍用標準MIL-A-46077F,該標準中除包括早期版本ELI級別的Ti-6Al-4V合金之外,增加了3個成分級別鈦合金,放寬了Fe、O元素含量的上限;將板材厚度規格擴大至100公釐;標準中增加了對板材縱向力學效能的要求,力學效能指標中不考慮厚度規格效應;規定Ti-6Al-4V合金板材的屈服強度不小於758兆帕,抗拉強度不小於827兆帕,伸長率指標不小於6%;規定了各厚度規格的板材抗彈效能(V50)指標。2006年,透過對軍用標準MILD-46077F的修訂,形成了新的裝甲鈦合金標準MIL-D-46077G。該標準中將裝甲鈦合金材料劃分為4個級別,即以航空級低間隙鈦合金材料為代表的1級、以商用鈦合金材料為代表的2級、以高含氧量的低成本鈦合金材料為代表的3級和以新型低成本鈦合金材料為代表的4級。
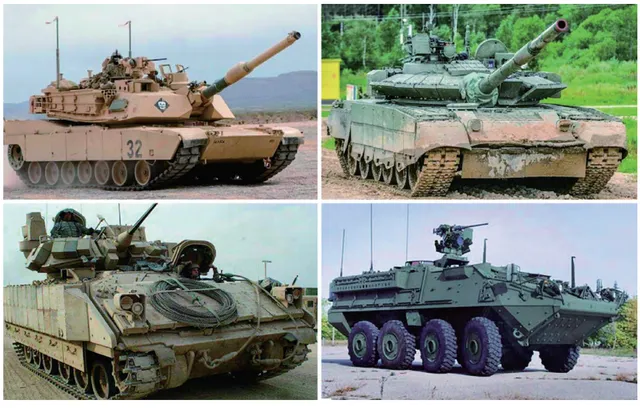
成本問題是關鍵
正如前文所述,要實作新一代坦克裝甲車輛高防護力輕量化的設計目標,擴大裝甲鈦合金材料的套用被認為是重要的技術途徑之一。更有觀點認為,裝甲鈦合金是新一代坦克裝甲車輛唯一可選材料。然而和鋼相比,裝甲鈦合金高昂的成本是其廣泛套用的最大阻礙,目前限制裝甲鈦合金在新一代坦克裝甲車輛上更大規模工程化套用的最大問題就是成本。近年來,世界主要鈦合金生產國包括美國、日本、俄羅斯、中國等,這些國家都開展了低成本鈦合金及其制備技術的研究。采用傳統工藝制備裝甲鈦合金板材,其成本構成中原材料約占45%,鑄錠熔煉約占20%,軋制成形約占27%,其他費用約占8%。 因此降低原料成本、縮短鑄錠熔煉與軋制成形等加工流程是降低裝甲鈦合金制造成本的有效途徑。使用廉價原材料(合金元素)的合金設計技術路徑主要是透過添加廉價的Fe元素以及放寬間隙元素O含量等途徑來降低成本,同時獲得良好的力學效能與抗彈效能。比如,美國Timet公司采用Fe元素代替V元素研發出低成本裝甲鈦合金Timetal62s(Ti-6Al-1.7Fe-0.1Si),其抗拉強度、屈服強度和斷後伸長率分別為1040兆帕、990兆帕和15%,並且成本比Ti-6Al-4V合金低約25%。 該公司還研發出低成本裝甲鈦合金TimetalLCB(Ti-1.5Al-6.8Mo4.5Fe),其冷加工和熱加工效能優異,力學效能與抗彈效能優於Ti-6Al-4V合金,並且成本比Ti6Al-4V合金低約22%。美國RMI公司采用適當放寬間隙元素O含量的方法制造出38.1公釐厚的低成本裝甲鈦合金Ti-6Al-4V-0.3O板材,其抗拉強度、屈服強度和抗彈極限速度分別為1014兆帕、931兆帕和1046公尺/秒,而相同厚度的Ti-6Al4V合金分別為972兆帕、883兆帕和1001公尺/秒;美國ATI公司采用Fe元素代替V元素以及放寬間隙元素O含量的技術,研制出低成本裝甲鈦合金ATI425(Ti-4Al-2.5V1.5Fe-0.25O),其力學效能與抗彈效能滿足軍用標準MIL-T-46077G的要求,成本比Ti-6Al-4V合金低約20%。除此之外,澳洲DSTO公司研發了低成本裝甲鈦合金Ti8Al-1Mo-1V,其密度低於Ti-6Al4V合金,力學效能和焊接工藝效能均占優;俄羅斯研發了低成本裝甲鈦合金VST3553+0.6Zr,其抗彈效能與Ti-6Al-4V合金相當。日本公司對低成本鈦合金研發也開展了大量的工作,Ti-Fe-O-N系列鈦合金是典型低成本鈦合金之一,該類合金采用O元素和N元素代替Ti-6Al4V合金的Al元素,Fe元素代替Ti6Al-4V合金的V元素,該合金可加工性良好,效能優異,成本明顯低於Ti-6Al-4V合金。在降低合金制造成本和減少損耗方面,日本發展了超塑性鈦合金Ti4.5Al-3V-2Mo2Fe,即SP-700鈦合金。該合金可以在低於800攝氏度溫度下采用超塑成形和擴散連線技術,超塑性成形溫度顯著低於Ti-6Al-4V合金,從而降低了生產成本。
改善加工特性的加工設計是降低裝甲鈦合金在新一代坦克裝甲車輛上更大規模工程化套用成本的另一個有效途徑。這實際上是指裝甲鈦合金的低成本合金化工藝技術。比如,美國陸軍在2004年的制造技術計劃中提出發展地面戰車用低成本高強度鈦合金材料技術的6年計劃,套用物件是未來戰鬥系統(FCS)車身和炮塔、「斯特賴克」戰車炮塔等裝甲件以及海軍陸戰隊新一代輕型裝甲戰車用結構件等。該計劃的主要內容是開發低成本的熔煉、鑄造、鍛造和焊接工藝技術,使鈦合金材料成本減少35%以上,主要制造成本減少50%。雖然作為計劃主體的FCS最終流產,但美國陸軍仍在返回料添加、冷床爐單次熔煉與扁錠直接軋制等裝甲鈦合金低成本制造技術方面取得了顯著進展,並實作了工程化套用。返回料添加是指,在鈦合金的生產過程中,由於其加工難度較大、成品率較低,會產生大量的殘料。其中,板材成品率為40%~70%,棒材成品率為50%~85%,管材成品率僅為20%~40%。鈦合金殘料主要包括切削殘料、塊狀殘料、長條狀邊角料、鑄錠帽口、圓餅殘料等,其成本約為海綿鈦的1/3。由於海綿鈦成本在鈦合金板材成本中約占40%,因此將鈦合金殘料回收處理後,在熔煉過程中作為返回料替代海綿鈦進行大量添加,可以大幅降低鈦合金原料成本。傳統鈦合金熔煉過程中普遍采用2~3次的熔煉,從而保證鑄錠品質以及合金成分的均勻性。美國首先開發了以電子束冷床爐(EBCHM)熔煉技術為代表的單次冷床爐熔煉技術。該技術能夠有效去除高密度夾雜、減少低密度夾雜、提高成分均勻性,因此可以在熔煉過程中大量添加返回料。同時,在鈦合金板材制造過程中,可以透過結晶器設計制備出扁錠直接用於後續軋制成形。大體來講,冷床爐精煉的主要優點有三:一是比較好地消除高密度和低密度夾雜,獲得細晶和組織均勻的錠坯;二是可100%地利用殘料作原料;三是對某些用途可一次熔煉成錠,生產扁錠、空心錠等,以減少板材與管材生產時的後續加工量。美國采用電子束冷床爐單次熔煉技術,制備出了12.7~76.2公釐的Ti-6Al4V鈦合金板材,並於2014年修訂了電子束冷床爐單次熔煉技術制備的板材標準AMS6945A【TitaniumAlloy,SingleMelt,Sheet,Strip,andPlate6Al-4VAnnealed】。美國陸軍研究評估了用於陸軍地面戰車的電子束冷床爐單次熔煉裝甲鈦合金Ti-6Al-4V板材,其拉伸力學效能和斷裂韌性不低於傳統工藝制備的裝甲板,且抗彈效能滿足美軍標MIL-DTL-46077F要求。另外,在鈦合金板材的制造過程中,采用電子束冷床熔煉制備的扁錠可直接進行軋制,省去了傳統工藝圓錠開坯、多火次鍛造等大量工序,大幅縮短了制造流程,降低了能耗與加工成本,並且制備的板材品質和效能穩定,提高了成品率。與「海綿鈦+真空自耗爐2~3次熔煉+多火次鍛造開坯+多道次軋制工藝」的傳統鈦合金板材制造技術相比,「返回料添加+冷床爐單次熔煉+扁錠短流程直接軋制工藝」的低成本制造技術,透過大量添加返回料可使原材料成本降低約40%,采用單次電子束冷床爐熔煉技術與扁錠直軋制短流程技術可以使材料損失降低約20%,人工和電力消耗降低約20%,綜合成本可以降低30%以上。還需要指出的是,發展精密鑄造技術,海綿鈦要在真空中電弧重熔,一般要經2次熔煉甚至3次熔煉才能得到純度和顯微組織適宜的鈦或合金。因此,透過(熔模)精密鑄造等近凈成形工藝來取代熔煉鑄錠(一般占鈦材總成本的15%)的工序成為降低成本的另一條有效途徑。連鑄連軋技術可以降低能耗、提高生產效率和產品成材率、改善產品均勻性,已成功用於鋼材和鋁材的生產。2014年,日本金屬材料研究所進行了鈦合金的連鑄連軋工藝的基礎實驗。研究表明,鈦具有優良的熱塑性和低的熱強度(1200K以上),高溫加工效能比鋼好,只要在相變溫度點以上不發生彎曲變形,就可用傳統的連鑄連軋裝置進行加工。這一研究成果進一步降低了裝甲鈦合金構件制造的工藝成本。
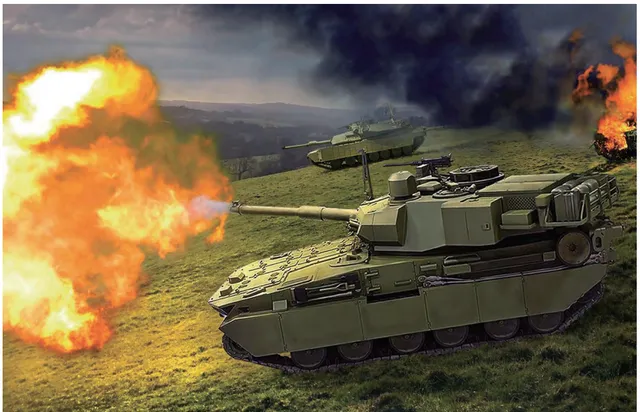
技術前景展望
業內主流觀點認為,下一代主力戰車,將戰鬥全重控制在50噸以內的輕量化控制是關鍵。然而,要令50噸以內的主力戰車,在防護力和戰場生存力方面仍要達到70噸級主力戰車相一致的水平,僅僅依靠軟防護手段和「戰利品」這樣的主動防護手段來進行防護增強是不夠的。在很大程度上,基本裝甲材料效能的進步是達到這一目標的重要保證。鈦合金材料作為典型結構車體主體材料,相比鋁合金材料在抗彈效能、承載效能、耐腐蝕效能、減重等方面具有顯著優勢,符合未來裝甲車輛的輕量化研制趨勢需要。目前,主要軍事工業國家已經開始嘗試用低成本裝甲鈦合金材料試制地面作戰平台車體。比如,BAE系統公司和GE公司各自推出了其以低成本鈦合金材料為基體裝甲和結構件的原型車。即BAE系統公司的油電混動輪式電動裝甲原型車「Pegasus」,其車首和車體框架使用低成本鈦合金焊接而成。GE公司的高機動性多用途輪式裝甲車原型車車體全部由低成本ATI425鈦合金焊接而成。但總體看來,國外鈦合金的套用與其他材料相比較仍然有差距,在坦克裝甲車輛上的套用還不是很廣,大型結構件還沒有套用鈦合金。這就說明鈦合金的效能、工藝和成本問題仍然是制約其套用的障礙,所以世界各國仍然在投入人力和物力開展鈦合金及其低成本技術的研究。前文說過,當前美國裝甲鈦合金軍用標準MIL-D46077G中,將裝甲鈦合金材料劃分為4個級別,從材料特性及發展套用情況來看,級別1主要用於航空結構主承力件,斷裂韌性很高,可達90兆帕/平方米以上,但是抗彈效能較低,美軍1994年以前試圖推廣用於裝甲結構件;級別2主要用於航空結構次承力件,斷裂韌性較高,可達50兆帕/平方米以上,但是抗彈效能不足,美軍1998年以前曾用於裝甲結構件;級別3主要用於裝甲結構件,抗拉強度較高,達950兆帕以上,並且抗彈效能良好,美軍1998年後開始套用於裝甲裝備;級別4是在級別3的基礎上研發,主要用於裝甲結構件,抗拉強度更高,達1050兆帕以上,並且抗彈效能優異。整體上,從美國裝甲鈦合金發展的趨勢來看,級別3與級別4為優選的裝甲鈦合金材料,其中,級別4中的高氧容限低成本裝甲鈦合金ATI425可實作大量添加返回料、電子束冷床爐單次熔煉與扁錠直接軋制技術進行制造,其成本較低、綜合效能良好、技術成熟度較高、工程化套用較廣。
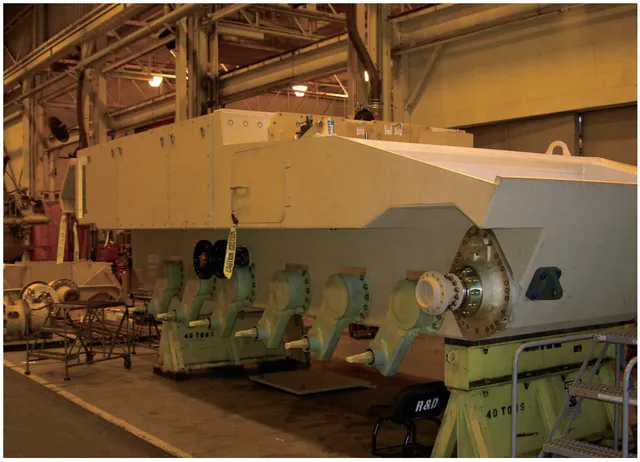
結語
鈦作為重要的稀有金屬材料之一,被廣泛套用於冶金、石油化工、醫療器械等各個領域。鈦金屬和鈦合金因密度小、比強度高、抗腐蝕性強,成為航空航天和兵器領域不可或缺、舉足輕重的材料。與傳統裝甲鋼相比,裝甲鈦合金是裝甲裝備改造升級和新一代裝甲裝備研制過程中實作輕量化與強防護的優選材料。當前,在各主要軍事工業國家,裝甲鈦合金低成本合金化技術和低成本制造技術方面取得了顯著進展,從而實作了在多種主力戰車、步兵戰車等不同型號裝甲裝備上的工程化套用。如在M1A2主力戰車上用鈦合金取代了七大鋼部件:回轉炮塔板、核戰、生物化學武器對抗系統護板、炮手主瞄準具罩、發動機頂蓋、炮塔樞軸架、指揮艙蓋、車長熱像觀察儀罩。用鋼制的這些構件的總品質1591千克,改為鈦合金之後,總品質下降到1116千克,減輕了近30%。M2步兵戰車的指揮艙蓋和頂部攻擊裝甲原是用鋁合金鍛造的,後改用100~127公釐Ti-6Al-4V合金板制造,攻擊裝甲則用80公釐厚的鈦合金板制造,它們的品質比鋼件的輕35%。但是,裝甲鈦合金的較高成本仍限制了其在裝甲裝備中的大規模工程化套用。目前日本、美國、中國、俄羅斯等國家都在大力發展鈦及鈦合金在裝甲防護的更大規模工程化套用研究,力爭研發出成本接近於裝甲鋁合金材料,能夠用於坦克裝甲車輛大部份結構件制造的裝甲鈦合金材料,從而為下一代裝甲地面作戰平台的研發鋪平道路。